Not everything needs your immediate reaction.
When do you know it’s the right time to do nothing?
Most front line leaders are action oriented. They want to jump in, they want to fix things, they want to make a decision or solve a problem. However, sometimes being action oriented can cause unintended consequences.
Remember, doing nothing is always an option.
I’m not endorsing procrastination or, as I like to call it, strategic deferral. In fact, sometimes just taking a moment to think things through will help you make better decisions. If you jump in and grab a wrench to fix the machine instead of thinking the problem through, there might be unintended consequences.
A plant manager once shared with me his experience when he gets a phone call in the middle of the night because a production machine is down and the team leader doesn’t know what to do.
Not everything needs your immediate reaction. Share on XHe said, “I’m always surprised that the frontline leader doesn’t have some basic information at hand. For example, if I’m trying to decide over the phone in the middle of the night what we should do, I want to know certain things. I want to know:
- What is the urgency on the order?
- Does it have to ship to the customer first thing in the morning or is it something that allows for a day of extra time if needed?
- Can we run it on a different machine?
- Is there a job running on that machine that could be deferred?
- What’s maintenance telling us?
- How long is this machine going to be down?
- Is this something we can quickly fix, but it might not run well, or do we need to shut it down for several hours to do a proper repair?
- Do we have the spare parts available?”
He says leaders need to gather that information so that they can make some of those decisions more often and better.
When you are strategically deferring or pausing before acting, you’re doing a few things.
You’re gathering information. You’re looking at different alternatives; not every alternative has the same level of desired outcomes. And part of the decision process is assessing risk. “Hey, the risk of running slow means our production numbers will be reduced, but at least we’ll complete the order for the customer.”
Sometimes you might consider experimenting. 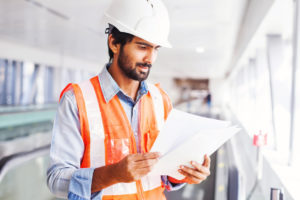
You might be thinking the tried and true method is the way to go. However, when you’re unsure what will work, experimenting might be the answer. And instead of jumping and grabbing the wrench to fix the machine yourself, maybe you should step back and get your team members doing some of that for themselves.
Simply slowing down, pausing, and sometimes doing nothing for at least a short period of time before you jump in, can help team members think for themselves and come up with solutions.